Company
The
necessity to increase productivity and quality control at production units opens the need for the development
of especial solutions. Namely customize tools, control equipment, manipulators
and automations.
MDU was created within this context.
Essentially by the demand for special production solutions for the
production line of Autoeuropa, a Volkswagen car factory located in Portugal, near Lisbon.
Now, with nine
years of experience on the conception and manufacturing of special equipments
the scope of our clients has increased. Presently, we still work in
innovation projects for several diferent markets, such as: automobile
industry, aeronautics, pharmaceutical, heavy industry handling systems,
software development, etc.
The continuous grouth of our
company leads to us to the acquisition of several manufacturing tools,
software and assembly installations.
Working method
MDU
supplies "turn key" solutions. For client demanded projects or coordinated
and developed together. Some projects start only with the need for a
solution. The design of the equipment to solve that solution arises with the
correct interaction between client and our project department.
Starting from the specifications the work follows the steps:
Mechanical, electrical, pneumatical and automation project
Manufacturing of mechanised parts
Acquisition of mechanical and electrical components
Assembly
Tests and presentation to client at out facilities
Assembly at client's location, stat up and baby sitting
Teaching of maintenance teams |
|
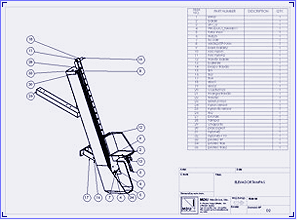
Main equipments are supplied with a operational
manual, including:
Drawings off all components
Maintenance instructions
List of spare parts
Electrical and pneumatical projects |
|
Objective
To assure the main priorities to the client the following steps are
considered:
Clear identification of client's specifications
Presentation of proposal
Definition of
a timing plan
Quality control during all the project, construction and assembly |
 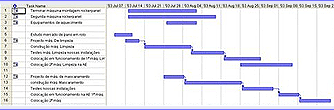 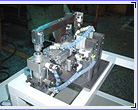
Project
The mechanical project is developed using Solid Works
design software.
Each part, component and assembly is designed using this software. This
technique allows the client to see the final solution before it is built. It
is possible to change the equipment before it is built. A significant cost
reduction is possible and turns the clients acceptance of the equipment
easier.
The same
approach is used to make special studies on existent equipments at the
client facilities. Allows to understand possible changes and investments.
For new products or simply to increase production or quality.
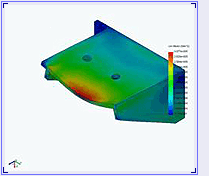 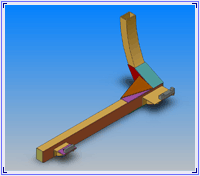 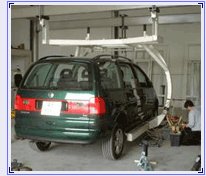
Stress analysis on line carriers doe to some design changes
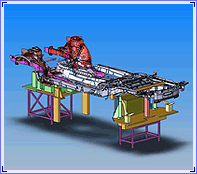 |
 |
Power train
assembly line |
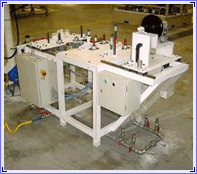 |
 |
Equipment to
assembly automatic gear boxes |
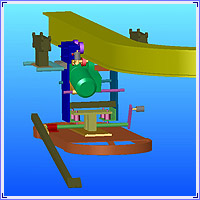 |
Motorised battery chargers |
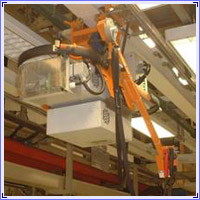 |
|
 |
 |
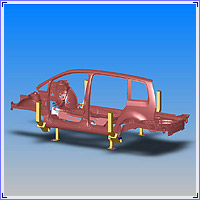 |
Line skids changed to work with
new model |
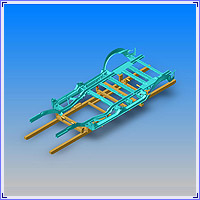 |
Production
The mechanical parts are
built at a
several MDU's
partners.
All the wending, assembly, electrical and pneumatical circuits are
done at our installations. Including tests and introduction to
client.
|